在汽车轻量化的大趋势下,众多汽车零部件企业大举进军汽车轻量化市场,这其中也涌现出一批行业佼佼者,江西豪斯特汽车零部件有限公司就是其中之一,他们通过扎实的热成形模具技术和优质的热成形零件产品,实现减轻车身重量、降低汽车的能耗,同时提升汽车的安全碰撞水平、为节能减排做出了重要贡献。
近期中国设备管理协会新能源汽车产业发展促进中心专访了豪斯特新能源结构件产品线总经理盛超。
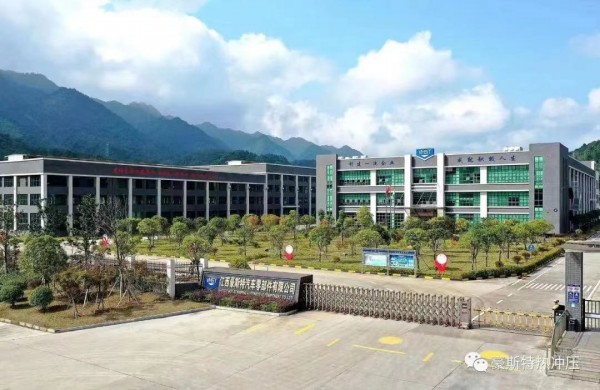
01
轻量化潮流
重量减一半,能耗降一半
重量减一半,能耗降一半
豪斯特盛超:目前,我国汽车零部件行业正朝着智能化、轻量化、模块化和环保化等方向发展。汽车的轻量化,是保证汽车的强度和安全性能的前提下,尽可能地降低汽车的整备质量,从而提高新能源汽车的动力性,减少能量消耗、降低排放污染、节省材料的同时降低成本。有研究表明,汽车重量降低一半,能量消耗也会降低将近一半。因此由于环保和节能的需要,汽车的轻量化已经成为世界汽车发展的潮流,这也是我们的机会所在。
02
又轻又安全
超强热成形技术拉高材料性能
豪斯特盛超:首先热成形技术作为一项先进的高强钢板成形技术,在减轻车身质量、满足车身零部件高强度需求及尺寸精度稳定等方面具有显著的优势。一般的高强度钢板的抗拉强度在400-450MPa左右,热成型钢是通过加热成形的硼钢,通过一系列处理后抗拉强度可提高至1300-2000 MPa。而根据我们现有的研发技术来讲,我们的超高强度热成型技术可以达到1500-2000 MPa,它可以在材料很薄很轻的情况下,满足汽车的安全需求。
除此以外,所有的热成形零部件都是一次成形。截止目前,我们已经和比亚迪、长城,吉利,领克、零跑、哪吒汽车等二十多家主机厂合作。同时我们在一体化天窗、前门环等有丰富的量产经验,后地板环、前后大门环等一体化技术应用上取得了重大突破。
03
底盘轻量化
降低电池壳体成本抢占市场
豪斯特盛超:在我看来,未来的新能源汽车可能都没有底盘了,直接将电池当作底盘来使用。前不久,特斯拉在柏林工厂研发出了一种全新的设计,那就是前铸造车身。特斯拉的Model Y前后车身都采用分段式的锻造设计。简单的来说,就是车头,车尾采用铸造技术生产,电池当作底盘来用,然后将车头车尾与电池连接起来,这样的好处就是整个车身结构重量将大幅减轻。最重要的是,减少了材料,也降低了焊接工艺,使得造车成本大大降低。
据我了解,目前主力新能源汽车均采用轻量化底盘件,特斯拉、MarvelX、比亚迪唐、蔚来等汽车均采用全铝的底盘结构。轻量化新能源底盘件产品包括铝制副车架、控制臂、转向节以及电池盒和支架等。
04
多技术集成
轻量化的同时降本增效
豪斯特盛超:现在整个市场变化非常快,随着特斯拉的降本,倒逼我们国内的新势力以及传统汽车都在往极致降本的方向去考虑。那么主机厂在降本的时候,就需要我们这种零部件模具供应商。我们的产品优势在技术,我们有20多年的技术积累,我们拥有冷冲、热压、辊压、焊接等整体方案能力,可以根据客户的需求,提供多技术集成化的方案。别人可能是单点的,但我们是集成整合式的,帮助主机厂降低成本的同时实现轻量化。我们通过超高强钢、超薄材料的使用,新技术的加成,来帮助我们的客户把材料变得更薄,强度更好,减轻重量的同时降低成本,也就是我们现在这种一体化的成型方式,这就是我们的优势。
此外,通过与国内大学研究机构的技术合作,我们在热冲压成形工艺技术、模具和装备等方面均取得了突破性的进展。经过多年的探索和积累,我们创建了一支专业、稳定、高效的自主研发队伍,主要专注于热成形新技术、新材料、新工艺的前沿研发。
关于豪斯特
江西豪斯特汽车零部件有限公司,是广东中泰工业科技股份有限公司(简称中泰科技)的控股子公司,是全球最大规模的热成形模具开发基地,是国内最早一批开展热成形技术开发与应用并实现量产的企业。

主要业务:电池包壳体研发和量产、冷热冲压模具研发和制造、冷热冲压零部件量产、冷热冲压零部件总成焊接等。现已为二十多家主机厂提供相关的配套服务。
精锐的模具设计团队:公司国内前列的热成形自主研发团队,均为拥有10年以上行业经验核心工程师,团队中80%为本科及以上学历。公司始终相信人才是第一生产力,也是解决客户需求最重要的保障。
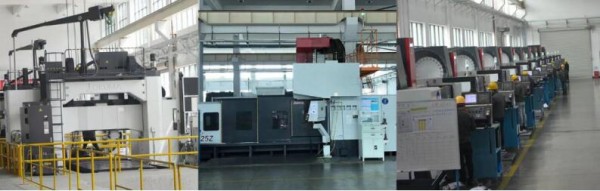
打赏
转载请注明出处。